Have a new part to prototype or need production run? We’ve got the manufacturing side covered start to finish. We can work from a drawing, 3D model, templates or existing part to create anything from a one-off to low-volume production runs.
Mold Making
direct from cad
Utilizing FDM (3D Printing) and CNC Router/Milling tools, we can turn a concept into a viable plug, or go straight to a mold, depending on the needs. All plugs and molds are created with an eye for detail in order to 1) make sure your part meets your dimensional and characteristic specifications and 2) ensure their repeated use where necessary.
by hand
If for some reason you don’t have a CAD model of the component you wish to make, our staff will work with you to determine if we would need to create it in house, or - if the part is simple enough - just cut molds from a sketch the old fashioned way.
In any case, we’re always trying to pick the best process to provide the highest quality component at the lowest reasonable cost, and ensure that you walk away delighted to have worked with us!
Part Manufacturing - Production Processes
Moldless
Moldless processes allow us to make one-off or very low volume designs without the expense of creating a mold. This consists of making a foam plug that is the shape of the part that is to be created, and a layup is then applied over this plug to create the final part.
Foam core - a foam block is hot wire cut, built up, or carved to net shape, with a composite skin laid up as specified to produce a strong, light weight component.
Lost foam - nearly the same process as foam core moldless construction, but with an added extra step to remove some or all of the foam from inside the part. Great for parts that consist of an enclosed shell where 2 or more molds would be required normally.
** With either method, the part can be laid up by hand, or vacuum bagged for best results.
Molded - open
Hand layup - The hand wet lay-up method is the simplest method for composite molding. Design changes are easy and low cost. Although it has a low production volume per mold, it is lower in cost and can be used for a wide range of part sizes.
Spray-up - Using spray-up or chopping is sometimes faster when producing more complex shapes because of its ability to conform. It is also a low cost method, though it suffers from a slightly higher weight penalty.
Molded - closed
Vacuum bagged - This method can be used for either a hand lay-up process or pre-impregnated lay-up. This method will remove any excess air and resin, and helps produce laminates with even consolidation, complete fiber wet-out, and improved core bonding.
Vacuum Infusion - Vacuum infusion (VIP) is similar to the vacuum bagging process, only the resin is infused after the pressure inside the bagged mold is lower than the atmospheric pressure. This method gives the lightest and strongest part - all things being equal - as well as the best surface finish without the use of a gel or epoxy shell coat.
SCRIMP™ (Seemann Composites Resin Infusion Molding Process) is a molding process - similar to VIP - that uses a vacuum to pull liquid resin into a dry lay-up and is used for making very high quality, repeatable composite parts. Typically this process is used when there is a sandwich core needed in the part.
Finishing
trimming
Parts can be handled several ways after demolding:
Sent rough - not recommended, but there are certain situations where a customer would want to dress the part themselves - be it for cost or assembly reasons.
Trimmed - Rough and fine trimming determined by customer requirements
Machined - If there are tight tolerances on a specific area of a component, we can use a variety of different machining techniques to get you what you need.
post-process finishes
Sometimes (though rare) it makes sense to apply a final finish after the part is demolded.
In-mold coatings (imc)
We’re able to apply many different coatings to parts in mold (depending on the process used).
Gelcoats (Clear and Pigmented - Polyester/Vinylester)
Epoxy Surface Coats (Clear and Pigmented)
Clear UV Stabilized Top Coats (Urethane, Polyester, Vinylester)
Pigmented Top Coats (Urethane, Polyester, Vinylester)
Primers (Urethane, Polyester)
Assembly
Got more than one component and don’t have the resources to put it all together? With the ever growing complexity of composite parts, it’s not uncommon for a customer to require receiving an entire sub-assembly. We can help with that too!
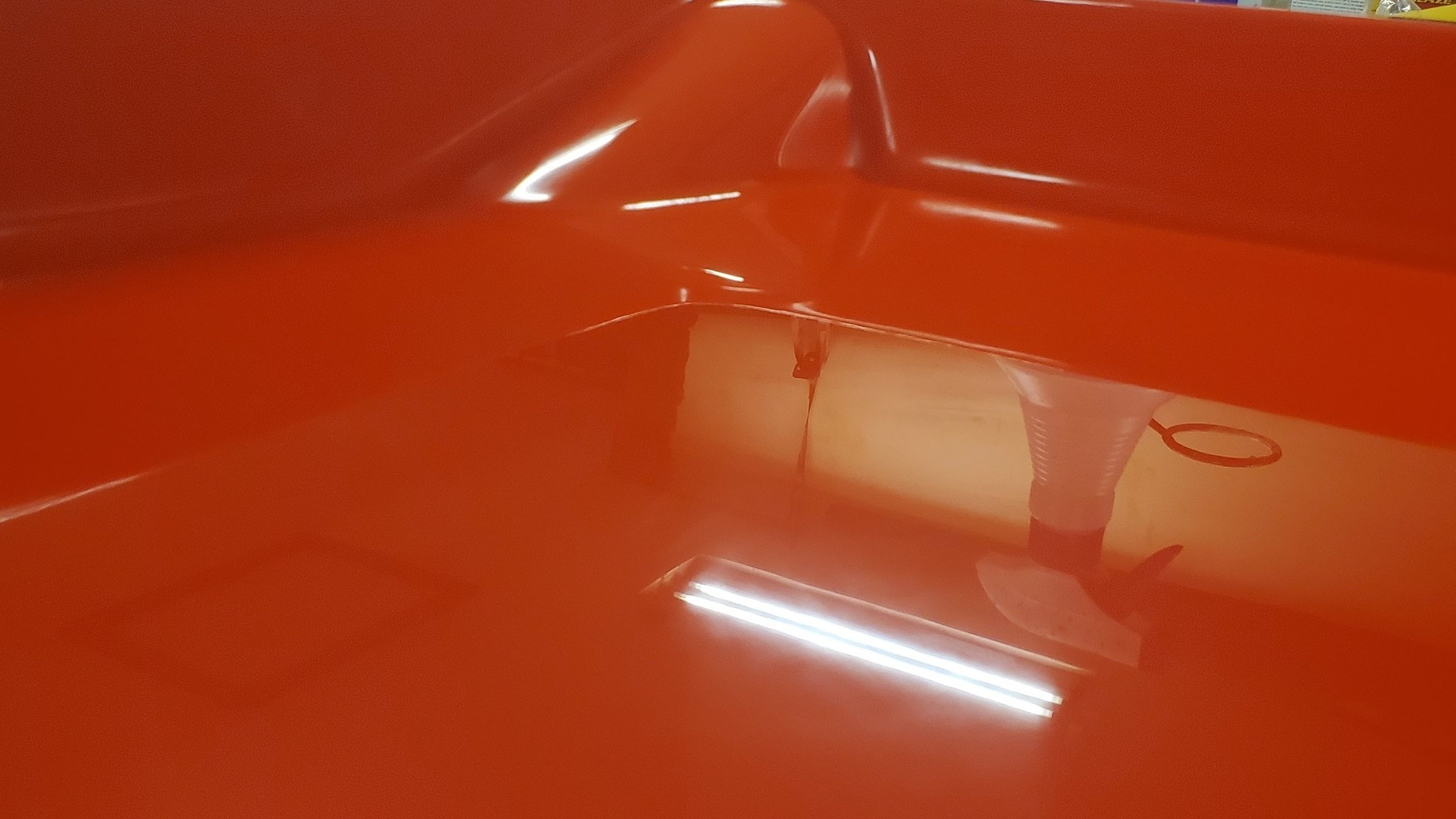
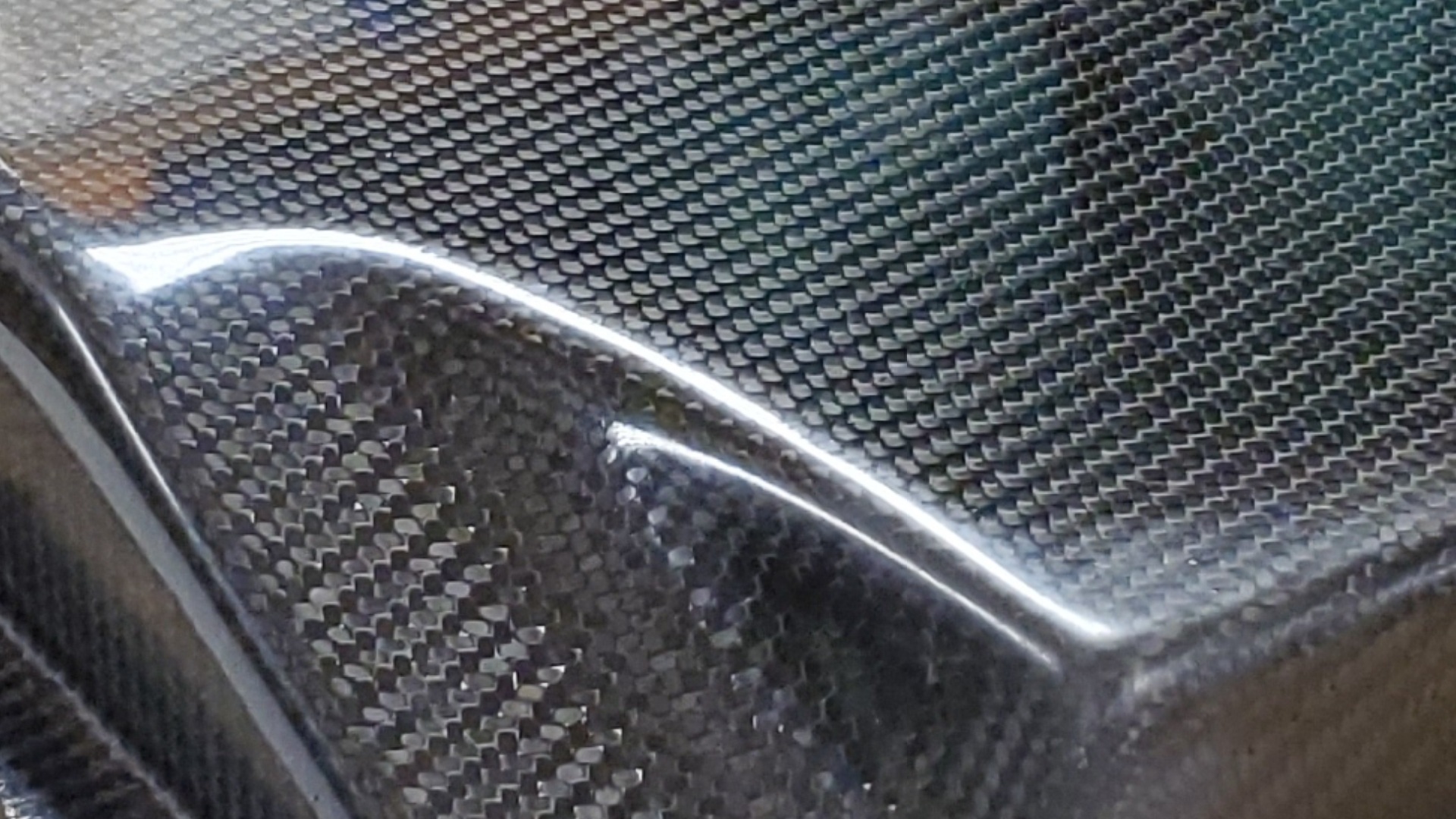
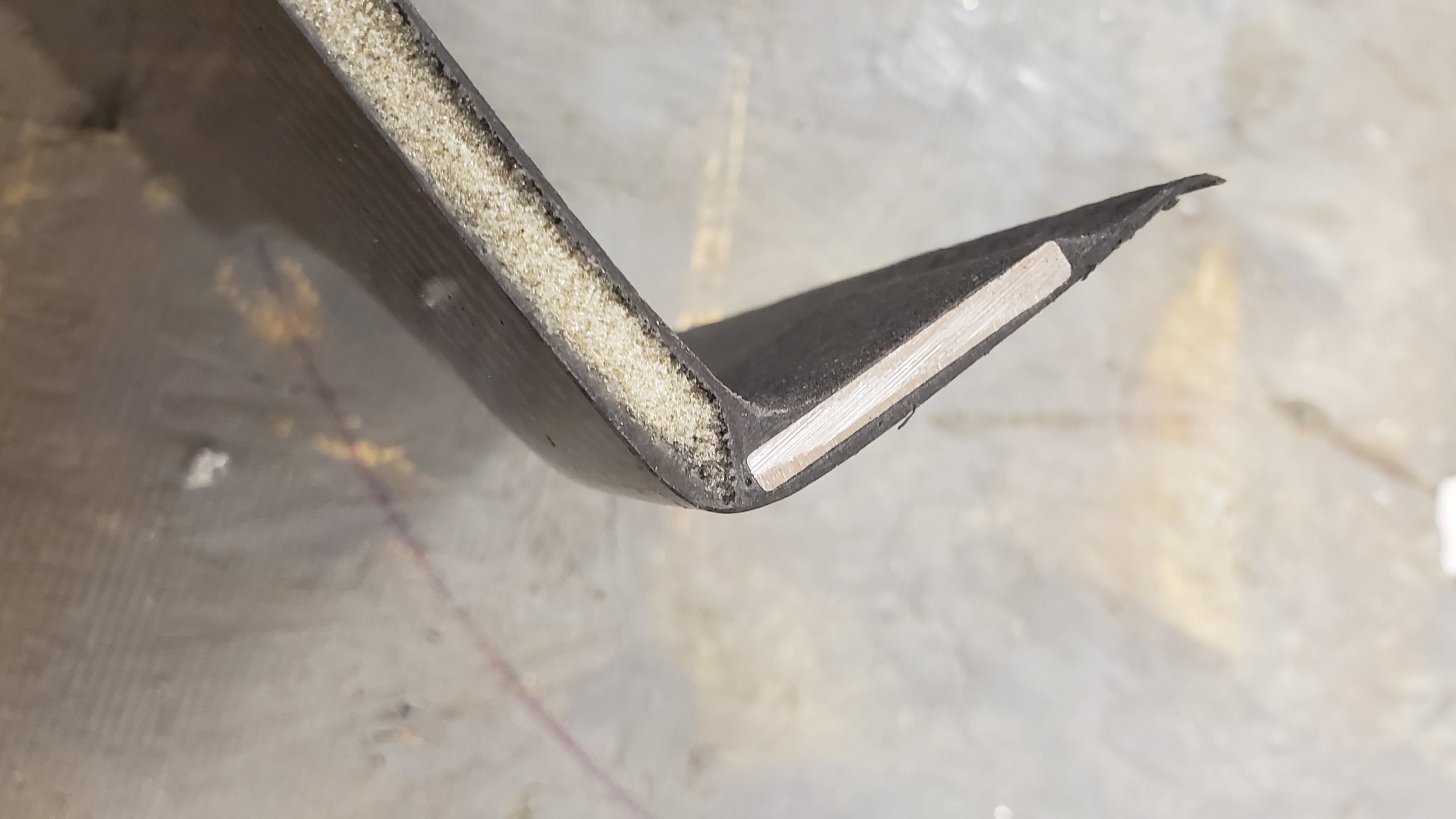